Power And Potential Of Hydrolic Press: An In-Depth Analysis
A hydrolic press is a machine that uses a hydraulic cylinder to generate a compressive force. It operates on the principle of Pascal's law, which states that pressure applied to a confined fluid is transmitted undiminished in all directions. This remarkable mechanism finds its applications in various industries, ranging from automotive to manufacturing, and has become a critical component in modern-day industrial processes.
In today's fast-paced world, the importance of efficient and reliable machines cannot be overstated. The hydrolic press stands out as a quintessential tool that offers both power and precision, making it indispensable in many sectors. From shaping metal parts to compacting materials, the versatility of the hydrolic press is truly impressive. Understanding its operation, design, and applications can provide valuable insights into its significance and the impact it has on our daily lives.
As we delve into the realm of hydrolic presses, it becomes essential to explore their various types, working principles, and safety measures. This comprehensive guide aims to shed light on every aspect of hydrolic presses, ensuring readers gain a thorough understanding of their functionality and applications. By the end of this article, you'll appreciate the ingenuity behind hydrolic presses and the pivotal role they play in industrial advancements.
Read also:Exclusive Insights On Brads Deal A Gateway To Incredible Savings
Table of Contents
- What is a Hydrolic Press?
- How Does a Hydrolic Press Work?
- Types of Hydrolic Presses
- Applications of Hydrolic Presses
- Advantages of Using Hydrolic Presses
- Disadvantages of Hydrolic Presses
- Key Components of a Hydrolic Press
- Why are Hydrolic Presses Important in Manufacturing?
- How to Maintain a Hydrolic Press?
- Safety Measures for Using a Hydrolic Press
- Innovations and Future Trends in Hydrolic Press Technology
- How to Choose the Right Hydrolic Press for Your Needs?
- Environmental Impact of Hydrolic Presses
- FAQs on Hydrolic Press
- Conclusion
What is a Hydrolic Press?
A hydrolic press is a machine designed to exert a significant amount of pressure on a small area using hydraulic fluid. The press consists of a large cylinder and a smaller cylinder connected by a pipe. When force is applied to the smaller cylinder, it gets transmitted to the larger cylinder through the fluid, resulting in a multiplied force output. This multiplication of force is what makes the hydrolic press such a powerful tool in various applications.
Hydrolic presses are commonly used in metal forming, molding, and assembly operations. They are known for their ability to apply consistent pressure, making them ideal for tasks that require precision and uniformity. The press can be used for tasks such as bending, stamping, and punching, allowing manufacturers to create complex shapes and designs with ease.
The origins of the hydrolic press can be traced back to the 18th century when it was first developed by Joseph Bramah. Since then, the technology has evolved significantly, and modern hydrolic presses are equipped with advanced features that enhance their efficiency and performance. Today, hydrolic presses are an integral part of the manufacturing industry, playing a vital role in the production of a wide range of products.
How Does a Hydrolic Press Work?
The operation of a hydrolic press is based on the principle of Pascal's law. This law states that when pressure is applied to a confined fluid, it is transmitted equally in all directions. In a hydrolic press, this principle is used to amplify force, allowing the machine to exert a tremendous amount of pressure.
The basic components of a hydrolic press include two cylinders: a master cylinder (also known as a pump) and a slave cylinder (the press cylinder). The master cylinder is filled with hydraulic fluid, and when force is applied, it pushes the fluid into the slave cylinder. Because the slave cylinder has a larger diameter, the force is multiplied, resulting in a significant amount of pressure on the material being pressed.
One of the critical aspects of a hydrolic press is its ability to regulate pressure precisely. This precision is achieved through valves and control systems that adjust the flow of hydraulic fluid. As a result, operators can control the force exerted by the press, ensuring that it meets the specific requirements of the task at hand.
Read also:Ultimate Guide To Fora Plural Insights And Understanding
Types of Hydrolic Presses
Hydrolic presses come in various types, each designed to cater to specific applications and requirements. Understanding the different types of hydrolic presses can help manufacturers select the right machine for their needs. Here are some of the most common types:
- H-frame presses: These are the most common type of hydrolic press, known for their versatility and ease of use. They consist of a horizontal frame that holds the cylinders and the workpiece.
- C-frame presses: These presses have a C-shaped frame, providing open access to the work area. They are ideal for tasks that require loading and unloading of materials.
- Four-column presses: As the name suggests, these presses have four columns that provide stability and support. They are used for heavy-duty applications that require significant force.
- Arbor presses: These are smaller, manually operated presses used for light-duty tasks such as pressing bearings or bushings.
- Transfer presses: These presses are used for high-volume production, allowing materials to be transferred between stations automatically.
Each type of hydrolic press has its unique advantages and is suited for specific tasks. For instance, H-frame presses are highly adaptable and can be used for a wide range of applications, while four-column presses are better suited for heavy-duty tasks that require high precision and stability.
Applications of Hydrolic Presses
The versatility of hydrolic presses makes them indispensable in various industries. They are used in applications ranging from metal forming to plastics manufacturing. Here are some of the key applications of hydrolic presses:
- Metal forming: Hydrolic presses are widely used in metalworking processes such as bending, stamping, and punching. They can shape metal sheets into complex designs with precision and consistency.
- Automotive industry: In the automotive sector, hydrolic presses are used for assembling components, forming body panels, and creating metal parts.
- Plastic manufacturing: Hydrolic presses are used in the production of plastic components through processes such as injection molding and thermoforming.
- Composite materials: Hydrolic presses are used to compress and shape composite materials, which are used in the aerospace and construction industries.
- Rubber products: Hydrolic presses are used to mold rubber products such as gaskets, seals, and tires.
The diverse applications of hydrolic presses highlight their importance in modern manufacturing. Their ability to apply consistent pressure with high precision makes them ideal for tasks that require accuracy and reliability.
Advantages of Using Hydrolic Presses
Hydrolic presses offer several advantages that make them a preferred choice in various industrial applications. Some of these advantages include:
- High force output: Hydrolic presses can generate a substantial amount of force, making them suitable for heavy-duty tasks.
- Precision and control: The ability to regulate pressure allows for precise control over the pressing process, ensuring consistent results.
- Versatility: Hydrolic presses can be used for a wide range of applications, from metal forming to plastic molding.
- Efficiency: Hydrolic presses operate with high efficiency, reducing energy consumption and operational costs.
- Safety: Modern hydrolic presses are equipped with safety features that protect operators and prevent accidents.
The advantages of hydrolic presses make them an invaluable tool in the manufacturing industry. Their ability to deliver consistent performance with precision and efficiency sets them apart from other types of presses.
Disadvantages of Hydrolic Presses
While hydrolic presses offer numerous benefits, they also have some disadvantages that should be considered:
- Initial cost: The cost of purchasing and installing a hydrolic press can be high, especially for large and complex machines.
- Maintenance requirements: Hydrolic presses require regular maintenance to ensure optimal performance and prevent breakdowns.
- Potential for leaks: Hydraulic systems are prone to leaks, which can lead to reduced efficiency and environmental concerns.
- Noise and vibration: Hydrolic presses can generate noise and vibration, which may require additional measures to mitigate.
Despite these disadvantages, the benefits of hydrolic presses often outweigh the drawbacks, especially in applications that require high precision and force.
Key Components of a Hydrolic Press
A hydrolic press consists of several key components that work together to generate force and perform pressing operations. Understanding these components can help operators and technicians maintain and troubleshoot the press effectively. The main components include:
- Hydraulic cylinders: These are the primary components that generate force by converting hydraulic fluid pressure into mechanical force.
- Pump: The pump supplies hydraulic fluid to the cylinders, creating the pressure needed for the press to operate.
- Valves: Valves control the flow of hydraulic fluid, allowing operators to regulate pressure and force.
- Reservoir: The reservoir stores hydraulic fluid and ensures a continuous supply to the pump.
- Frame: The frame provides structural support for the press and holds the components in place.
- Control system: Modern hydrolic presses are equipped with electronic control systems that allow for precise control over the pressing process.
Each component plays a critical role in the operation of a hydrolic press, and regular maintenance is essential to keep the press running smoothly and efficiently.
Why are Hydrolic Presses Important in Manufacturing?
Hydrolic presses play a pivotal role in the manufacturing industry due to their ability to deliver high force with precision and reliability. They are used in a wide range of applications, making them indispensable in various sectors. Here are some reasons why hydrolic presses are important in manufacturing:
- Versatility: Hydrolic presses can be used for a multitude of tasks, from metal forming to material compaction, making them a versatile tool in manufacturing.
- Precision: The ability to control pressure with precision ensures consistent results, which is essential for maintaining quality standards.
- Efficiency: Hydrolic presses operate with high efficiency, reducing energy consumption and operational costs.
- High force output: The ability to generate significant force allows hydrolic presses to handle heavy-duty tasks that other machines cannot.
The importance of hydrolic presses in manufacturing cannot be understated. They contribute to increased productivity, improved product quality, and reduced operational costs, making them a valuable asset in modern industrial processes.
How to Maintain a Hydrolic Press?
Regular maintenance is essential for ensuring the optimal performance and longevity of a hydrolic press. Proper maintenance can prevent breakdowns, reduce downtime, and extend the life of the machine. Here are some key maintenance practices for hydrolic presses:
- Inspect hydraulic fluid levels: Regularly check and maintain hydraulic fluid levels to ensure efficient operation.
- Check for leaks: Inspect the system for any signs of leaks and address them promptly to prevent loss of efficiency.
- Lubricate moving parts: Regularly lubricate moving parts to reduce friction and wear, ensuring smooth operation.
- Inspect seals and hoses: Check seals and hoses for wear and damage, and replace them as needed to prevent leaks.
- Test safety features: Regularly test safety features to ensure they are functioning correctly and providing adequate protection.
By following these maintenance practices, operators can ensure that their hydrolic press operates efficiently and safely, minimizing the risk of breakdowns and extending the life of the machine.
Safety Measures for Using a Hydrolic Press
Safety is a critical consideration when operating a hydrolic press. Proper safety measures can prevent accidents and protect operators from injury. Here are some essential safety measures for using a hydrolic press:
- Wear appropriate personal protective equipment (PPE): Operators should wear safety glasses, gloves, and other PPE to protect themselves from hazards.
- Ensure proper training: Operators should receive thorough training on the safe operation and maintenance of the hydrolic press.
- Follow manufacturer's guidelines: Adhere to the manufacturer's guidelines and safety instructions to ensure safe operation.
- Regularly inspect safety features: Test and maintain safety features such as emergency stop buttons and guards to ensure they function correctly.
- Keep the work area clean: Maintain a clean and organized work area to reduce the risk of accidents and injuries.
Implementing these safety measures can help create a safe working environment and prevent accidents when using a hydrolic press.
Innovations and Future Trends in Hydrolic Press Technology
The field of hydrolic press technology is continuously evolving, with new innovations and trends shaping the future of the industry. These advancements aim to enhance the efficiency, safety, and versatility of hydrolic presses. Here are some of the key innovations and future trends:
- Automation: Automation is becoming increasingly prevalent in hydrolic press technology, allowing for more precise and efficient operation. Automated systems can reduce human error and increase productivity.
- Advanced materials: The use of advanced materials in manufacturing hydrolic presses can improve durability and reduce weight, leading to more efficient operation.
- Energy efficiency: Manufacturers are focusing on developing energy-efficient hydrolic presses that consume less power and reduce operational costs.
- Smart technology: The integration of smart technology, such as sensors and IoT connectivity, allows for real-time monitoring and diagnostics, improving maintenance and reducing downtime.
- Customization: Customizable hydrolic presses can be tailored to meet specific requirements, providing flexibility and adaptability for various applications.
These innovations and trends are set to revolutionize the hydrolic press industry, offering significant benefits in terms of performance, efficiency, and safety.
How to Choose the Right Hydrolic Press for Your Needs?
Selecting the right hydrolic press for your needs is crucial for ensuring optimal performance and efficiency. Here are some factors to consider when choosing a hydrolic press:
- Application: Consider the specific tasks and applications for which the press will be used. Different types of presses are suited for different applications, so it's important to choose one that meets your requirements.
- Force requirements: Determine the force needed for your tasks and select a press that can generate the required pressure.
- Size and capacity: Consider the size and capacity of the press, ensuring it can accommodate the materials and workpieces you will be using.
- Budget: Consider your budget and evaluate the cost of purchasing, installing, and maintaining the press.
- Safety features: Ensure the press is equipped with adequate safety features to protect operators and prevent accidents.
By considering these factors, you can select a hydrolic press that meets your specific needs and requirements, ensuring efficient and reliable operation.
Environmental Impact of Hydrolic Presses
Hydrolic presses, like many industrial machines, have an environmental impact that should be considered. Understanding these impacts can help manufacturers implement measures to reduce their environmental footprint. Here are some environmental considerations related to hydrolic presses:
- Hydraulic fluid disposal: Proper disposal of hydraulic fluid is essential to prevent environmental contamination. Used fluid should be disposed of according to environmental regulations and guidelines.
- Energy consumption: The energy consumption of hydrolic presses contributes to their environmental impact. Energy-efficient models can help reduce energy use and lower emissions.
- Material use: The materials used in manufacturing hydrolic presses can have environmental implications. Using sustainable materials and recycling components can help reduce the environmental impact.
By implementing environmentally friendly practices and selecting energy-efficient models, manufacturers can reduce the environmental impact of hydrolic presses and contribute to a more sustainable industry.
FAQs on Hydrolic Press
- What is the primary use of a hydrolic press? Hydrolic presses are primarily used for shaping, forming, and compacting materials in various industrial applications, including metal forming and plastic manufacturing.
- How does a hydrolic press differ from a mechanical press? A hydrolic press uses hydraulic fluid to generate force, allowing for precise pressure control, while a mechanical press relies on mechanical components such as gears and levers to generate force.
- What safety precautions should be taken when operating a hydrolic press? Operators should wear appropriate PPE, follow manufacturer's guidelines, and regularly inspect safety features to ensure safe operation.
- Can hydrolic presses be used for light-duty tasks? Yes, hydrolic presses are available in various sizes and can be used for both heavy-duty and light-duty tasks, such as pressing bearings or bushings.
- What are the key components of a hydrolic press? The key components of a hydrolic press include hydraulic cylinders, a pump, valves, a reservoir, a frame, and a control system.
- How can the environmental impact of hydrolic presses be reduced? The environmental impact can be reduced by using energy-efficient models, properly disposing of hydraulic fluid, and using sustainable materials in manufacturing.
Conclusion
Hydrolic presses are a vital component of the manufacturing industry, offering unparalleled force, precision, and versatility. Their applications span various sectors, from metal forming to plastic manufacturing, making them indispensable in modern industrial processes. Understanding the operation, types, and applications of hydrolic presses can provide valuable insights into their significance and impact.
By considering factors such as force requirements, size, and safety features, manufacturers can select the right hydrolic press for their needs, ensuring efficient and reliable operation. Furthermore, implementing proper maintenance practices and safety measures can enhance the longevity and safety of the press, minimizing the risk of accidents and breakdowns.
As the field of hydrolic press technology continues to evolve, innovations and trends such as automation, energy efficiency, and smart technology are set to revolutionize the industry. By embracing these advancements, manufacturers can improve efficiency, reduce environmental impact, and contribute to a more sustainable future.
4 Life: A Guide To Health, Well-being, And Longevity
Mastering The Dynamics Of The Group Of Eight: Insights And Impacts
Innovative Trends And Strategies In Hive Fitness

Proctor Silex, Panini Press & Compact Grill
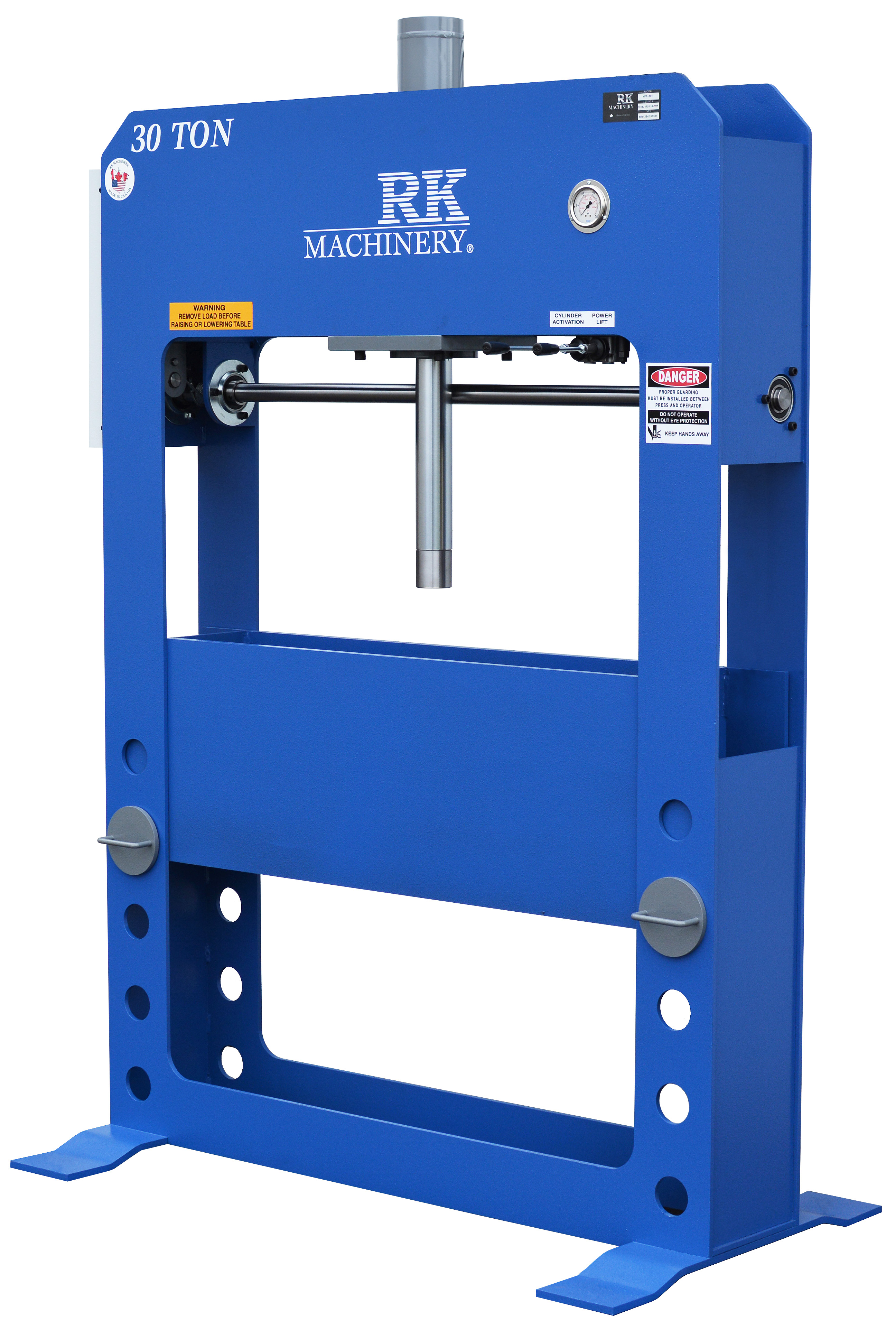
H Frame Hydraulic Press 30 Ton RK Machinery